As our planet continues to warm because of climate change, technologies that were once considered luxuries, like air conditioning (AC) in our vehicles, are now considered essential standards. AC systems like the ones we use today were first introduced into cars and trucks in the 1960s. They are based on vapor-compression technology that is over 100 years old and requires chemical refrigerants to operate. These chemicals are not friendly to the environment. To address this issue, the U.S. Department of Defense (DOD) is funding a project led by Ames National Laboratory scientists to develop a new type of AC system based on elastocaloric cooling technology that requires no harmful refrigerants.
The DOD is in pursuit of better options for air-conditioning military vehicles because of supply chain and safety issues. The vapor cooling technology in traditional AC systems require specific chemicals, which people generally call Freon™, to create the cooling reaction. The actual chemicals used have changed over the years, because of the harm they cause to the ozone and climate. Today, it is most common to use hydrofluoroolefin-1234 (HFO-1234yf) in automotive AC, which has less of an effect on global warming than previously used chemicals.
HFO-1234yf is better for the environment, but it is also flammable and comes with a risk of sustained burning, making it unsuitable for use in military vehicles. The shift to using HFO-1234yf also means that older chemicals are being phased out of commercial use, making them difficult to find. These challenges have motivated the DOD to find alternatives to chemical refrigerants for AC devices.
As part of this effort, a team of scientists from Ames Lab, led by Julie Slaughter, Ph.D., received funding to develop an elastocaloric AC device that can be used in military vehicles. This project would provide an AC option that is entirely safe for the environment, is more efficient than current vapor-cooling systems, and is not flammable.
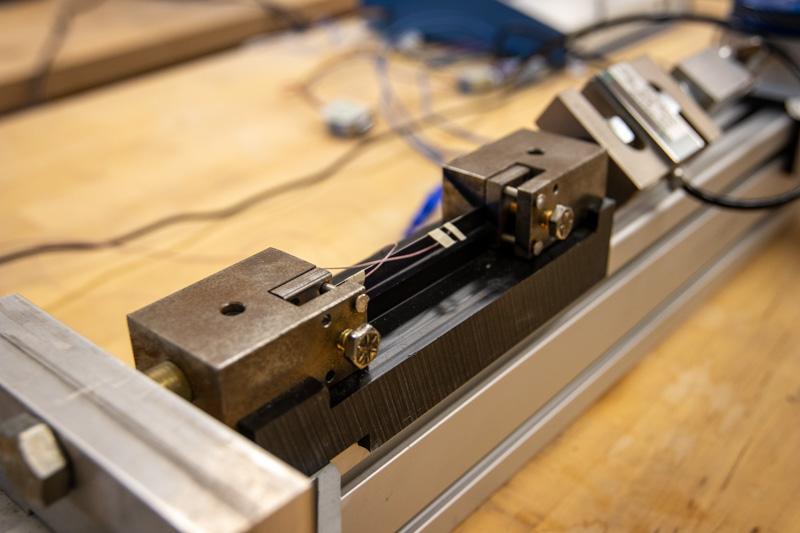
Elastocaloric cooling is based on materials that respond to both stress and temperature in unique ways. These materials are shape memory alloys (SMA), and they have an important quality called superelasticity. SMAs can be deformed when they are cold and then hold this shape until heated above a certain temperature. Superelasticity is the ability to undergo large deformations under stress and return to its undeformed shape when the stress is removed.
Superelasticity is the effect that makes elastocaloric cooling possible; as it undergoes large deformations, the SMA releases heat. The most common elastocaloric material in use is an alloy made of nickel and titanium called nitinol, which stands for Nickel-Titanium Naval Ordinance Laboratories. It is typically used in applications such as flexible eyeglass frames and medical stents.
The temperature change in these superelastic materials is the basis for elastocaloric cooling. When a stress is applied to or removed from the material, it initiates the phase transition and the related temperature change. “We’re capturing the energy from that temperature change,” said Slaughter. “So that is how we use it to heat and cool things.”
“Normally, if you take a metal and you stretch it, the force gets bigger as you stretch it more. For superelastic materials, you stretch it a little bit, and then, all of a sudden, it just moves with very little added force,” Slaughter explained. “The material is going through a phase transition when it does that and when that phase transition happens, you also release heat, which causes a temperature change.”
For cooling, this process is reversed. Removing tension from the material causes it to absorb heat and provide a cooling effect. This effect can transfer to any fluid in contact with the material. The cold fluid can then remove heat from another area, such as the cabin of a vehicle, thus working like an air conditioner.
The team is developing their AC system using nitinol, which is readily available because it is widely used in the medical industry. But for this application, it needs to be optimized for low energy losses and large temperature differences. They are working closely with their industry partners, ATI Specialty Alloys and Components and G.RAU Inc., to evaluate and optimize the material for cooling applications.
To create a successful cooling system, both materials development and system design are necessary. Therefore, in addition to their work on the nitinol, the team is building an active regenerator. Slaughter explained that while nitinol is capable of very large temperature changes (as much as 25°C or 77°F), it breaks when operating at the high stresses needed. At small stresses it can last longer, however, the temperature change is only around 5°C. To be effective for cooling there needs to be a temperature change of roughly 25°C. So, by flowing water-based fluid through a system, heat can be stored and released. Multiple regenerators working together are needed to make a device with the necessary temperature span that works as well as existing vapor compression devices.
This elastocaloric system will be more environmentally friendly than current AC devices since it will use the solid cooling material and water-based fluids without any harmful chemicals. It will be more efficient than current vapor-compression-based devices and will not pose a risk of sustained burning.
“I see this project as a good first step,” said Slaughter. “Then it could also move into other uses for air conditioning and cooling and heating. It's got a lot of potential.”
The work is being funded by the U.S. Department of Defense’s Strategic Environmental Research and Development Program (SERDP). The partnership between Ames National Laboratory and ATI Specialty Alloys and Components and G.RAU Inc is governed by a Cooperative Research and Development Agreement (CRADA).
Ames National Laboratory is a U.S. Department of Energy Office of Science National Laboratory operated by Iowa State University. Ames Laboratory creates innovative materials, technologies, and energy solutions. We use our expertise, unique capabilities, and interdisciplinary collaborations to solve global problems.
Ames National Laboratory is supported by the Office of Science of the U.S. Department of Energy. The Office of Science is the single largest supporter of basic research in the physical sciences in the United States and is working to address some of the most pressing challenges of our time. For more information, please visit https://energy.gov/science.